Recently IFMA Workplace Evolutionaries’ Chicago HUB and Work Design Magazine held an in-person event at the Haworth/Chicago showroom.
In this interactive conversation, panelists and attendees explored office furniture from a circular economy (CE) perspective and the insights gained were so valuable, we’ve recapped them up here.
In a circular economy, products and materials are kept in circulation through processes like maintenance, reuse, refurbishment, remanufacture, recycling, and composting.
– Ellen MacArthur Foundation
In our current linear economy model, office furniture is designed, manufactured, procured, and utilized without an integrated plan for a next life. While decommissioning, take back and recycling programs divert some furniture from landfills, discarded office furniture is still a major contributor. The US EPA estimated in 2018 that 17 billion pounds of office assets go to landfills each year, (Peters, 2023).
For context, the diagrams below illustrate the Linear Economy with the “take, make, waste” model where products are (by lack of design) discarded after the first or second use. And a Circular Economy approach where products are designed for long-term use/re-use and re-purposing.
A View from the Office Furniture Trenches
Moderated by Cynthia Milota, Director of Workplace Strategy at Ware Malcomb, the panelists represented corporate real estate/JLL; a not-for-profit trade association for the business furniture manufacturers/BIFMA; a SaaS database of green certifications/Ecomedes and a leading sustainable furniture manufacturer/Haworth.
The conversation began with challenges the audience experienced with circular economy furniture solutions including:
New furniture is just easier.
There’s a perception problem with remanufactured furniture.
Internal re-use is hard as the left hand doesn’t know what the right hand is doing.
Other factors included additional time and coordination complications, perceived greater costs, zero internal incentives and the inertia to change. There was considerable mystery surrounding how to start and who can help which our expert panelists addressed.
Begin with the End in Mind
Panelists offered a strategy to get started. First, establish a playbook or BAU (business as usual) requirements that integrate CE goals with the business and procurement processes. With the expansion of corporate ESG (Environment, Social, Governance) reporting, there is a new level of accountability. Second, seek partnerships with team members and vendors so that all are working toward the same goals and metrics. There’s an emerging value on existing furniture stock, not solely based on first cost or disposal value. Existing furniture, built to last, has a high embedded carbon score. This new math and values-based accounting associated with furniture is being integrated into ESG planning and reporting.
Understanding your organization’s objectives will guide in prioritizing where to start. Ecomedes’ Paul Shahriari offered his top 6 list:
- Return on Investment
- Energy Savings
- Water Savings
- Human Health
- Carbon Reduction
- Circular Economy
Maintaining a transparent line of communications with internal and external stakeholders is essential for documenting and sustaining progress. JLL’s Annalise Dum advocated for starting the communications as early as possible. Avoiding rampant greenwashing, panelists discussed how circularity stories based on real metrics build trust and accountability.
Considering Asset Management Software, which are “tools that helps organizations track and manage their assets throughout the entire asset life cycle, from acquisition to disposal,” (Novak, 2023). These enable organizations to maximize use of furniture assets. Vendors of this SaaS (software as a service) model included Rheaply and Reseat.
Furniture as a Service (FaaS) is an emerging trend in the US. In this model, an organization essentially rents furniture at a recurring fee (generally considered an operational expense) with the option to return or exchange products as the workplace evolves. While more prevalent in Europe, US companies seeking material and energy efficiency, reduction in materials consumption and carbon offsetting are exploring this model. Beyond the CE benefits, FaaS offers old-fashioned flexibility and adaptability, with the option to update (read change out) your furniture as your business and employee preferences evolve.
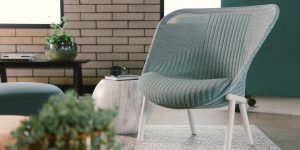
Many furniture manufacturers are making big strides in product-level emission reductions strategies. For example, Haworth’s Katie Chapman shared that in the case of the Haworth Cardigan lounge chair, the foam is produced using a biomass-balanced process, which replaces traditional fossil fuel-based energy sources with biological fuel sources during production. Biomass-balanced foam reduces embodied carbon in the foam production process by 80%.
Future legislation impacting the CE and furniture is about 5-10 years out, as estimated by BIFMA’s Steve Kooy. His work on Capitol Hill advocating for the furniture industry and specifically circular sustainable solutions expects laws to be enacted on a state by state basis. For example, the forever chemical PFAS (the chemical found in stain regardant products) used in carpets, rugs and after-market treatments has been banned in 8 states, with more taking action.
The final thought
Getting started can be overwhelming but panelists suggested selecting just one metric per year and track it. Make it simple, then report and celebrate it. Then next year add a second metric. Ultimately, you’ll want to build a story and communicate to your audiences.
Special thanks to the Haworth team for coordinating and hosting this event and to Work Design Magazine’s publisher Michelle Weiss for promotion and for this follow-up article.
References
MacArthur, E. Foundation, “What is a Circular Economy,” Retrieved from: https://www.ellenmacarthurfoundation.org/topics/circular-economy-introduction/overview#:~:text=The%20circular%20economy%20is%20a,remanufacture%2C%20recycling%2C%20and%20composting.
Novak, J., (November 2023), “5 Best Asset Management Software Of 2023,” Retrieved from: https://www.forbes.com/advisor/business/software/best-asset-tracking-software/
Peters, A., (July 2023), “How Office Furniture Recyclers Divert a Growing Pile From Landfills,” Retrieved from: https://www.costar.com/article/184294338/how-office-furniture-recyclers-divert-a-growing-pile-from-landfills