Mimaristudio gives Pelsan Tekstil a new space to develop, socialize, share, and be inspired.
Project Overview:
- Design Firm: Mimaristudio
- Client: Pelsan Tekstil
- Completion Date: January 2023
- Location: Tekirdag, Turkey
Pelsan Tekstil, a part of the Hassan Group, Turkey’s first breathable polyethylene film manufacturer serving the medical, hygiene, and insulation sectors, has a new head office designed by the Mimaristudio team.
The goal of the project was to create a living space suitable for the corporation’s innovative, technological, and colorful world in the new working area located at the heart of the company’s new production facility. Flexibility, variability, transparency, and experience were the main keywords that served as the starting point for the design of the space.
The project aimed to create a collaborative workspace, development, and living space by providing the necessary physical and social conditions for creativity and productivity while supporting communication and interaction among employees. A living space was designed for Pelsan employees to develop themselves, socialize, share and be inspired.
In addition to the interior design of the building, the facade design was also carried out by Mimaristudio. Terrace floors that allow users to access the outdoors were among the striking details of the building, considering the effects of the previous epidemic. With these living spaces, a semi-transparent connection is established between the indoor and outdoor areas. This interface also allows visual contact between the users of the space and the outside world with its different-sized openings.
The landscaping work referring to the “Nature in Space” step in the biophilic design approach is another important feature of the façade. The natural landscape areas created on the facade interface allow controlled progress of greenery that will eventually envelop this interface over time. The selected plant cover provides an opportunity to see the color, texture, and structural changes of nature on the interface during seasonal transitions.
In the interior design, a design language was developed suitable for each floor’s structure and different needs. The entrance floor was planned as a shared workspace with flexible usage where local and foreign guests could be hosted, different-sized meetings could be held, and, at the same time, a point of intersection providing access to the factory production area and R&D laboratory. With the guidance provided from this floor to the lower floor, a dining area was planned where factory and office employees could use together, as well as guests. The area, which can be used for work, rest, and hosting needs at different times of the day, is also one of the socializing areas inside the building.
The workspace was designed with a flexible planning approach, while all employees except for unit directors were planned to work in an open office. Employees were given the freedom to choose where, when, and how they work. Short break areas were planned where brief meetings could be held by walking along the circulation axis that connects the administrative and engineering departments. As much as the program allowed, flexibility of use was added to the entire floor with socialization areas that everyone can freely use, individual and collaborative working, meeting, and discussion spaces in different scales, functions, and forms.
On the other hand, being environmentally friendly and sustainable were also important components of the design approach. In this context, the project included the concepts of “Nature in Space”, “Natural Reminders”, “Nature of Space”, and the 14 biophilic design paths under these headings, which are part of the “biophilic design” approach.
At the end of the day, the building is used not only as a workspace but also as a living space, reflecting the employer’s innovative, environmentally friendly, and colorful corporate identity, with a focus on employee well-being.
Project Planning
The project started with the request and needs program received from the employer after the first meeting. Shortly after, Mimaristudio designed a survey where all employees could share their expectations and opinions. Due to the pandemic, questions related to pandemic measures were also included in the survey. As a company that operates at full capacity even during the pandemic, a planning and design process was carried out that prioritized employee health and well-being. The goal was to create a building that could be used jointly by both factory workers and administrative staff, enabling them to share and interact with each other.
Project Details
Mimaristudio’s proposal prioritized well-being, offering a safe space that provides collaboration opportunities while allowing employees who spend long hours in enclosed spaces and are dependent on technology to be physically and mentally healthy and happy. In this context, a living space was designed where all employees inside the building can work with maximum daylight, regular clean air, appropriate thermal and acoustic comfort conditions, appropriate lighting solutions, and technological opportunities.


Using the right colors in workspaces increases employees’ performance, productivity, and satisfaction. For this reason, in the project, colors that do not overwhelm the space, do not make users feel cramped, and are correct, timely, and in balance were preferred.
The issues of “silence” and “quiet working environment”, which are the biggest problems of workspaces, were carefully addressed with the acoustic measures planned during the design process. In addition to preventing sound transmission between enclosed rooms, suitable materials and products were preferred for open space employees to have the necessary comfort conditions. Here, the “Make-up” family of acoustic ceiling and wall products developed by Feltouch, designed by Ayça Akkaya Kul, and the “Ra” acoustic lighting family, which is used for the first time in this project, are among the prominent products in the space.
Although the building has a very rich natural light opportunity, the lighting design that supports natural light was another issue addressed by the Mimaristudio team. In the project, LED technology was preferred with priority given to energy efficiency, and a balanced and human-centered lighting design was prioritized within each floor’s own physical structure. Technical lighting products were preferred for general lighting, and decorative products were also included in the project. Especially, the “Sade” lighting, designed by Ayça Akkaya Kul and produced by Maiizen, which is handmade and produced with double-walled technique by inflating, draws attention.
Products
- Acoustic Panels: Feltouch
- Acoustic Wallpaper: Evist
- Modular carpet tiles: Shaw Contact
- Modular LVT looselay tiles: Tarkett Desso
- Porcelain Ceramics: Kale / Edilcuoghi Edilgres K.Beige
- Ceramics: Vitra
- Glass / Glazing Walls: Trimline
- Decorative painting: Novacolor (Navdecor) / Keim (Letoon)
- Acoustic Lighting: Feltouch
- Technical Lighting: Lamp83
- Decorative Lighting: Sade (Maiizen) / Artemide, Cosmic Angel, Suspension / Italamp, Baffo Suspension, cromo / Luceplan Bulbullia / Luceplan Ecran / Grok Invisible
- Sanitary solutions: Vitra-Artema / Bocchi

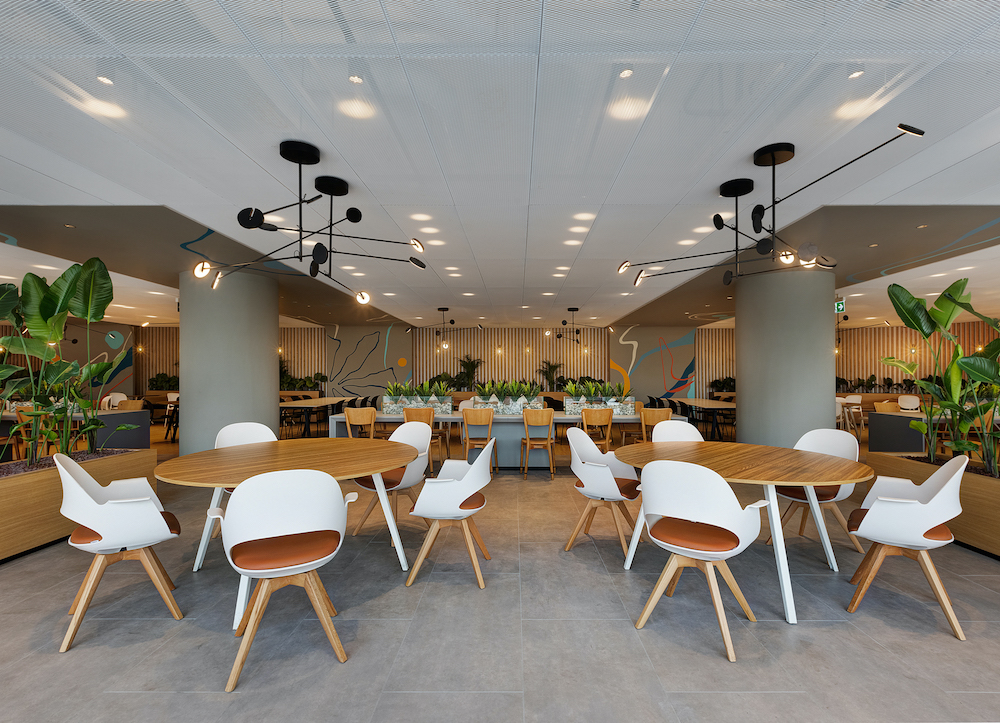
Overall Project Results
The change management design process was successfully carried out in full collaboration with the employer. The Pelsan team was also involved in the process with extensive participation. The project and field implementation work coinciding with the pandemic posed some difficulties in the procurement of certain building materials and in the timing and budget planning, but the process was successfully completed with proper risk management.
While some meetings were held face-to-face, others were organized remotely. The project was well received due to its focus on employee health and well-being, creating a sense of belonging and privilege for the users, arousing curiosity in every individual who comes or doesn’t come to the building, and reflecting the Pelsan identity as a living space that outsiders would want to be a part of.
Project Summary
- General Contracting: Oguz Bayazit Mimarlik
- Facade Work: Metal Koza
- Facade Glass Work: Sisecam
- Creative Graphic Design: Monroe
- Mural Artist: Gamze Yalcin
- Mechanical Project: Arkon
- Mechanical Work: Aldem, Noma
- Electrical Works: Frekans
- Custom Millworks: Nankontrat / Odabas
- Custom Millwork Materials: Kapsan / Yildiz Entegre / AGT
- Contract and loose furniture: Nurus / Addo / Ersa / Connection Turkey / Hamm / Marwood
Design Team
- Mimaristudio Designers: Ayca AKKAYA KUL and Önder KUL
- Project Team: Kaan GÜLKIRAN and Enver KUDA