Ware Malcomb’s Director of Sustainability, Erica Godun, highlights a path to sustainable workplace design in the era of circularity, where architects and designers champion repurposing, reclaiming, and reimagining materials, ultimately crafting environmentally responsible spaces for a brighter future.
Designers are always looking for the next fabulous thing. Beautiful, iconic, classic, edgy and new. We want our spaces to stand out, so we highlight recently developed and technically superior products that last longer, clean easier and provide flexibility. Sustainability has thoroughly permeated commercial architecture and design. Designers encourage product manufacturers to include recycled content, lower VOCs, streamline manufacturing processes and track embodied carbon. We source these sustainable options with great intention, include them in our projects, bask in the glow of appreciative clients and move on to the next project. The challenge is that most materials will end up in a landfill during the next renovation. How can we avoid this?
Early strategies for carbon reduction focused on reducing emissions with operational energy efficiency. As those strategies mature and expand, the focus is shifting to embodied carbon. The Carbon Leadership Forum defines embodied carbon as “greenhouse gas emissions arising from the manufacturing, transportation, installation, maintenance and disposal of building materials.” So, by making less and reusing more, we reduce embodied carbon. That leads us to the idea of a circular economy or circularity.
Key tenants of a Circular Economy model include:
- Eliminating waste and pollution
- Circulating products and materials (at their highest value)
- Regenerating nature
(source: https://www.ellenmacarthurfoundation.org/topics/circular-economy-introduction/overview)
The United States is a consumer culture. We seek convenience and efficiency. It’s often faster and easier to buy something new than to repair or refurbish it and keep it in use. Even the idea of one person’s trash being another’s treasure is typically limited to one-to-one transactions on Facebook Marketplace, Craig’s List or eBay. However, this mindset is slowly changing, and opportunities for efficiently implementing circular strategies are becoming available for commercial workplace design.
Deconstruct, Don’t Demolish
The first circularity concept to embrace is reuse; the least carbon-intensive form of reuse is repurposing what already exists.
Who doesn’t love designing in a completely demolished space?
Designers can tailor wide-open areas to the tenant’s needs with nothing to impede creative expression. We must learn to embrace adversity, love complexity and treat every obstacle as an opportunity. All the walls likely don’t need to be removed, and repurposing some rooms can be an option. Enhance those reused spaces with new paint, flooring and light fixtures.
The next step in reuse is to keep materials at the same location – no shipping required. The walls may have to come down, but the doors and frames can be reused. Look around and see what can be salvaged for the project. If you can’t use the doors, someone else probably can. Are the light fixtures energy efficient? Be creative in redistributing them. Are there millwork pieces in good condition? Surely, there’s a place for some cabinets. No one ever said they had too much storage. There may be additional design costs, which can be offset by not having to buy new materials.
Instead of demolition, find a contractor who will decommission and deconstruct instead. This process of carefully disassembling building components for reuse takes longer than sending in a team with sledgehammers and may be costly. If the time factor is understood early, it can be worked into the schedule, not impacting the project’s completion. Costs can be offset with sales of the salvaged materials or tax benefits of donations. Even salvaging limited materials for recycling can make a difference. Many commercial carpet manufacturers have take-back programs, and like Bentley’s FULFILL, they will take any carpet, even if it’s not theirs. Tarkett’s ReStart take-back and recycling program will also take back any type of flooring from any manufacturer and it includes a partnership with a company in the automotive industry that is able to use ground LVT in their manufacturing process. USG and Armstrong will take old ceiling tiles to feed their manufacturing process.
Project Spotlight: Ware Malcomb completed an interior renovation of Bellevue Brewery in Washington. The décor within the space uses reclaimed Douglas Fir salvaged from historical buildings such as the old University of Washington Police Station and from covered bridges in Sweet Home, Oregon. Not only did these materials serve the circular model and reuse, but they also paid homage to the local area.
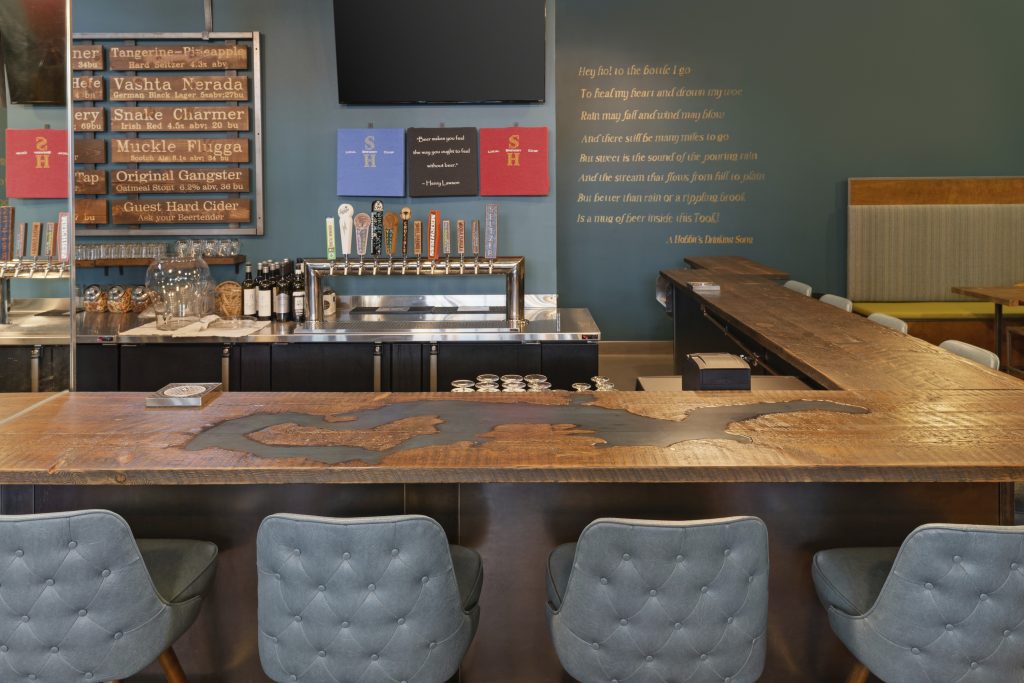
Purposeful Material and Product Specification
As you dive into the design process, consider the value of reused and refurbished materials and appreciate the character they could bring to the project. There will be opportunities for statement pieces and standard materials. A day of antiquing might get you that perfect accent piece, and when time doesn’t allow for that, companies like Doors Unhinged can provide reclaimed doors, frames and hardware. Where does Doors Unhinged get its products? For a tip, go back three paragraphs. I hope you’re starting to see the circle.
Remember those walls and rooms left in place to save money (and reduce carbon)? If they were movable, it would have been easier to reuse them, and you could put them where they best served the design rather than work around them. Rather than drywall and studs with added finishes, there are modular construction options like DIRTT and Falkbuilt. Modular construction systems are manufactured offsite and brought to the site for assembly. This results in less waste in construction, potentially shorter construction timelines, and infinite future possibilities that don’t involve the landfill.
Of course, not everything can be reused. When specifying new materials, consider their total embodied carbon – it is not just in their initial manufacture but their entire life cycle. Align a material’s durability with its likely use life. Think ahead to the next renovation and include options that are easily separated for reuse or recycling for areas on a quicker cycle. Use more durable items for building elements that are less likely to change. For the sake of brevity, I won’t review all the considerations for sustainable material selection, but there are many great resources available. The Metropolis Climate Toolkit has information for those just starting their sustainable journey and reminders and tidbits for those deep in the green materials trenches.
Full Circle
Closing the circle will be a team effort. There’s no easy button yet, but the options are out there. Designers must embrace the possibilities and communicate that positive attitude to clients.
We should design with the intention of leaving a positive legacy for future generations by making every choice matter – whether it’s specifying materials, renovating an existing building, or encouraging sustainability choices with our clients.
“Circularity” is not just trendy terminology but a mindset shift. Architects and interior designers should partner with clients to design and deliver environmentally sustainable and socially responsible spaces. We can build a more sustainable and resilient future by integrating circular strategies.
Interested in more insights from Erica Godun?
Why ESG Should Influence How We Design Spaces
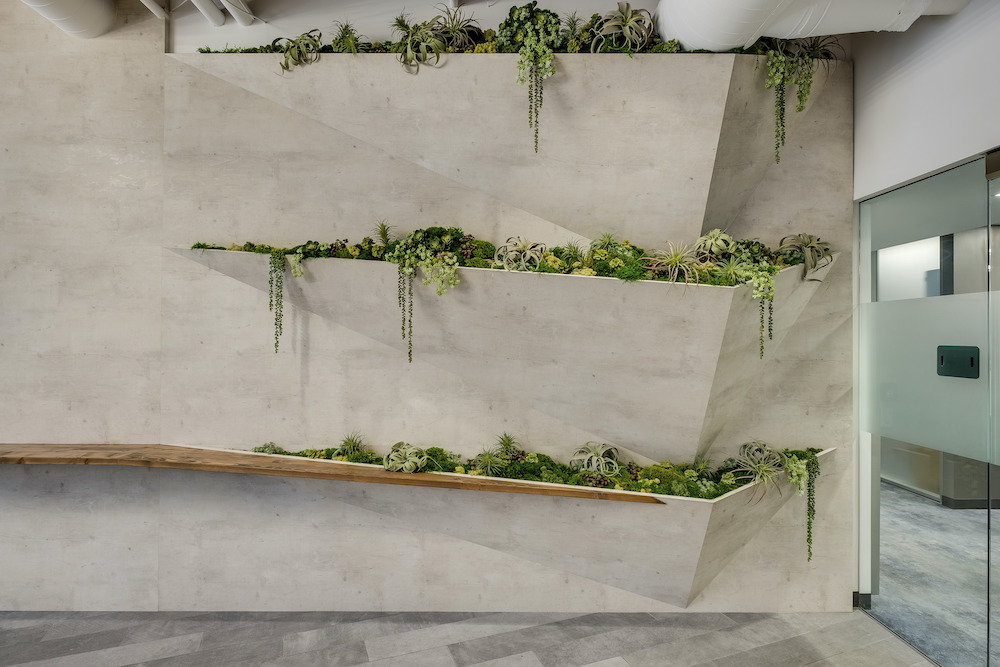